M9 / M11 Long range thermal imaging PTZ EOIR FLIR security camera capabilities and executive summary
PTZ THERMAL IMAGING FLIR CAMERAS PRODUCT SELECTION:
SPI Long Range thermal imaging camera Modular Open Architecture System design supports both new and legacy platforms and applications;
and provides a seamless upgrade path as requirements and technologies change. Our goal is zero
obsolescence, at a system level, and the lowest cost over the life of the program or platform. We aim to
achieve this goal while providing users with the capability to deploy the latest and best sensor technology
available.
Our modular design concept using true line replaceable units can simplify maintenance and support capability
upgrades in the field. This capability eliminates the need for any special tools or equipment. Our gimbal
systems minimize the use of external cables to simplify system integration and reduce potential failure points.
All of these aspects combined result in a sustainable long term approach to your long Range thermal imaging camera systems.
SPI provides innovative and cost-efficient solutions to support the most complex Long Range electro-optical imaging
applications, utilizing modular system design that is easy to integrate, configure, upgrade, and service. Our
products include the design and manufacturing of high-precision two-axis stabilized gimbals, EO-IR system
integration, COTS EO-IR long range PTZ FLIR thermal imaging mobile force protection, coastal and border solutions, laser range finder LRF systems
fabrication, and full high definition (HD) IR (full HD Visible) EO tracking systems.
When the mission hinges on synchronizing multiple sensor suites tracking multiple targets from a variety of
remote geographical locations, we incorporate an intuitive Command and Control graphical user interface,
high precision mechanical and electronic assemblies, and an open architecture interface to work seamlessly
with existing networks.
The SPI Team is made up of experts in the fields of electrical and mechanical engineering, optical
design and analysis, IR thermography, 3D solid modeling (CAD/CAM), and precision machining and assembly.
SPI’s Long range thermal imaging FLIR PTZ security camera systems are currently utilized by US Customs and Border Patrol, US Marine Corps, US Air Force, US
Navy, US Department of Homeland Security, NASA, the Panama Canal, the South Korean Navy, Saudi Aramco Oil, and MIT Lincoln Labs.
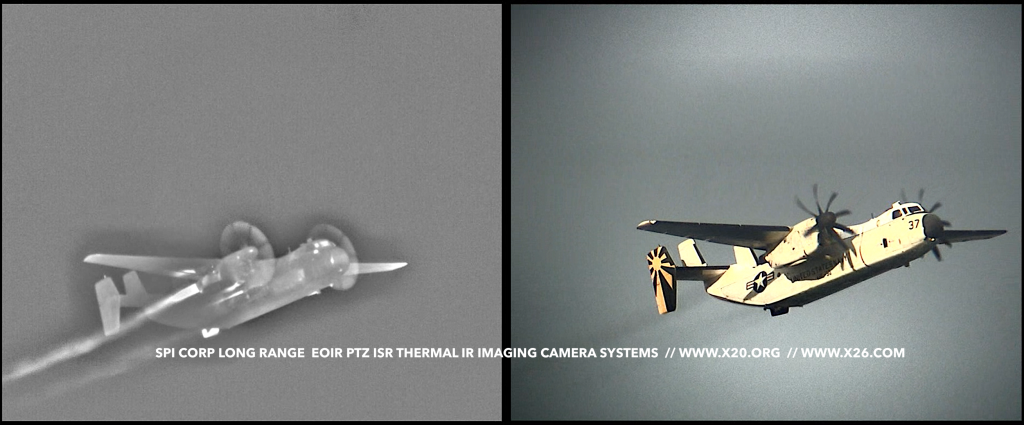
WHY THE SPI LONG RANGE THERMAL IMAGING PTZ FLIR CAMERA SYSTEMS ARE THE BEST CHOICE FOR LONG RANGE CAMERA PROJECT
Modular Open Architecture System objectives
• Support both new and legacy platforms and applications
• Provide a seamless upgrade path as requirements and technologies change
• Our goal is zero obsolescence, at a system level, and the lowest cost over the life of the program or
platform
• We aim to achieve this goal while providing users with the capability to deploy the latest and best
sensor technology available.
• Design system modules as true line replaceable units to simplify maintenance and support capability
upgrades in the field.
• Eliminate the need for any special tools or equipment
• Eliminate or reduce the need for sensor alignment after replacement
• Maximize the use of captive fasteners for all LRUs to support installation in extreme and challenging
environments
• Minimize the use of external cables to simplify system integration and reduce potential failure points
Lowest Cost Over the Life of the Program
• Zero system level obsolescence moving forward based on the ability to integrate new sensor
technology as it is released
• Allows engagement of Legacy and New Sensors: Reverse Compatible to legacy sensors, or a
combination of long range thermal imaging EOIR new sensors and legacy sensors as spares
• Forward compatible from SD to full HD, as new sensors are introduced
• No wear components
• EOIR long range thermal imaging Sensors and Gimbals sealed within Aluminum Weldments or Carbon Fiber sealed IP 68 plus enclosures which are full immersion tested.
• Very High industry leading MTBF
• Uses standard Ethernet or Serial C2 connections
• Code for new sensors upload-able remotely into the on-board FPGA from system Ethernet connection
• Rapid upgrades saves time and material costs
• Rapid Sensor changes reduce labor and down time
• Streamlined integration effort minimizes schedule and technical risk
• This approach drives the cost down for each platform over the life of the Program while at the same
time still remaining competitive at initial purchase cost for each system.
KEY CONSIDERATIONS
• DIRECT DRIVE SERVO MOTORS AND ENCODERS DIRECTLY CONNECTED TO THE AZIMUTH AND
ELEVATION DRIVE SHAFTS SUPPORT THE FULL RESOLUTION OF THE 19 BIT ABSOLUTE ENCODERS WITH
NO HYSTERESIS
• BRUSHLESS MOTORS AND OVERSIZE BEARINGS PROVIDE HIGH RELIABILITY, EXCELLENT ALIGNMENT
RETENTION AND SIGNIFICANT STRUCTURAL MARGIN
• THERE ARE NO WEAR OR LIMITED LIFE COMPONENTS IN THE SYSTEM THAT REQUIRE SERVICE OR
MAINTENANCE
• SUPERIOR DESIGN & LONG TERM RELIABILITY
OUR HARDWARE PROPOSAL
PROPOSAL FOR EO / IR, VISUAL & THERMAL CAMERA COMBO GIMBAL SYSTEM
The M9 LONG RANGE PTZ THERMAL IMAGING FLIR CAMERA SYSTEM
The M9 is a Long Range high-performance, high-definition pan and tilt system that is ideal for day/night
surveillance over long ranges in the harshest of conditions. The M9 Long Range thermal imaging ptz system was designed with the specific
intent to support the highest performance sensors available. HD video data is transmitted with a high-speed
fiber optic connection, with no compression or data loss. In addition to the standard suite of high
performance imaging sensors, the M9’s HD’s gimbal can accommodate additional optional sensors,
including laser rangefinder, laser pointer/designator, laser zoom imaging illuminator, and many other devices.
SYSTEM FEATURES & BENEFITS:
360° azimuth, continuous rotation
Direct drive servo motors
Superior HD image processing
Extreme zoom range with HD resolution
HD resolution imaging in extreme environments
Remote updating, GPS-referencing, dual HD-SDI outputs
Optional gyro stabilization for tower, mast, marine vessel & vehicle applications
HD Long Range thermal flir imaging & EO CCTV video tracking options
Integrated system controller: controls all motion & sensors via a single Ethernet connection (this allows
for changing sensor types without re-coding the user C2 interface)
Rugged design thrives in the harshest of environments
HD LONG RANGE THERMAL MWIR CAMERA FEATURES:
Auto focus & fine focus
Electronic image stabilization
Turbulence mitigation
HD resolution, 1280 x 1024 Pixels, 15μm pitch
Edge enhancement & contrast enhancement
200-1,200 mm Coated Hardened Continuous Optical Zoom Germanium Lenses
LASER POINTER FEATURES:
Eye safe at the aperture
15km range
4Hz flashing mode and 30Hz continuous mode
LASER RANGE FINDER FEATURES:
20km Long range LRF
Eye safe at the aperture
Solid state design for long life
LONBG RANGE HD DAYLIGHT CAMERA
ASSEMBLY FEATURES
• 0.009 lux ½” HD CMOS 2.2 MP
• High speed auto focus
• Heat haze/wave removal &
image stabilization
• Black glass (low pass filter) for NIR Imaging
LENS OPTIONS
• 16.7-2000mm zoom Long Range Visible HD camera with optical
stabilized lens
• 16.7-2000mm zoom Long Range Visible HDTV camera
M11 MODULAR LONG RANGE THERMAL IR IMAGING FLIR PTZ EOIR CAMERA SYSTEM
The M11 Is A Long Range Modular Gimbal System which is an agile system for medium
payloads — a yoke-style gimbal design for today’s challenging tracking applications. Because the payload is
supported over the azimuth axis, the result is both faster response and greater accuracy. This integrated
sensor system combines our industry-leading gimbal with cutting edge Long Range Thermal infrared and HD visible sensors. These
systems can accommodate a wide range of laser pointers, Custom Long Range NIR, SWIR Optics, LRF laser range finders and laser illuminators.
SYSTEM FEATURES:
• 360° azimuth, continuous rotation
• Direct drive servo motors for maximum accuracy (within 0.0006°)
• Over-the-azimuth payload design provides low inertia for high speed tracking capability
• Blind mate connectors provide rapid installation or re-configuration in the field
• High resolution imaging achieved in extreme environmental conditions with heat haze & fog mitigation
• Fully network enabled for integration into existing IP surveillance networks
• Optional gyro stabilization for tower, mast, marine vessel and vehicle applications
• Proprietary design provides the lowest operational cost over the life of the system
• Image stabilization
• Rugged design thrives in the harshest of environments
For the single payload day camera gimbal we recommend 3 pcs of the following:
M11 Long Range MWIR Cooled IR Camera with an Ultra Long range EO payload.
The Visual EO camera payload would be as follows:
HD DAYLIGHT CAMERA
ASSEMBLY FEATURES
• 0.009 lux ½” HD CMOS 2.2 MP
• High speed auto focus
• Heat haze/wave removal & electronic
• Image stabilization
ng • Black glass (low pass filter) for NIR Imaging
• Turbulence, Haze, Clutter and fog Mitigation
• LENS OPTIONS
• 16.7-2000mm zoom Long Range Visible HD camera with optical
• stabilized lens
Overview
Lowest Cost Over the Life of the Program
• Zero system level obsolescence moving forward based on the ability to integrate new sensor
technology as it is released
• Allows engagement of Legacy and New Sensors: Reverse Compatible to legacy sensors, or a
combination of new sensors and legacy sensors as spares
• Forward compatible from SD to full HD, as new sensors are introduced
• No wear components
• Long Range Sensors and Gimbals sealed within Aluminum Weldments or Carbon Fiber sealed IP 68 plus enclosures
which are full immersion tested
• Very High industry leading MTBF
• Uses standard Ethernet or Serial C2 connections
• Universal Radar Absolute Position Feedback for Slue to Cue
• Code for new sensors upload-able remotely into the on-board FPGA from system Ethernet connection
• Rapid upgrades saves time and material costs
• Rapid Sensor changes reduce labor and down time
• Streamlined integration effort minimizes schedule and technical risk
• This approach drives the cost down for each platform over the life of the Program while at the same
time still remaining competitive at initial purchase cost for each system.
KEY CONSIDERATIONS
• DIRECT DRIVE SERVO MOTORS AND ENCODERS DIRECTLY CONNECTED TO THE AZIMUTH AND
ELEVATION DRIVE SHAFTS SUPPORT THE FULL RESOLUTION OF THE 19 BIT ABSOLUTE ENCODERS WITH
NO HYSTERESIS
• BRUSHLESS MOTORS AND OVERSIZE BEARINGS PROVIDE HIGH RELIABILITY, EXCELLENT ALIGNMENT
RETENTION AND SIGNIFICANT STRUCTURAL MARGIN
• THERE ARE NO WEAR OR LIMITED LIFE COMPONENTS IN THE SYSTEM THAT REQUIRE SERVICE OR MAINTENANCE
IMAGES
The M9 cooled thermal imaging systems can be integrated with Radars for long range tracking and slue to cue capabilities